Mike McMahon is the President of Getac North America. Mike is experienced in the rugged OEM computing business on both end user and channel side. His unique perspective on rugged technology spans Enterprise, Public Safety, and Federal markets.
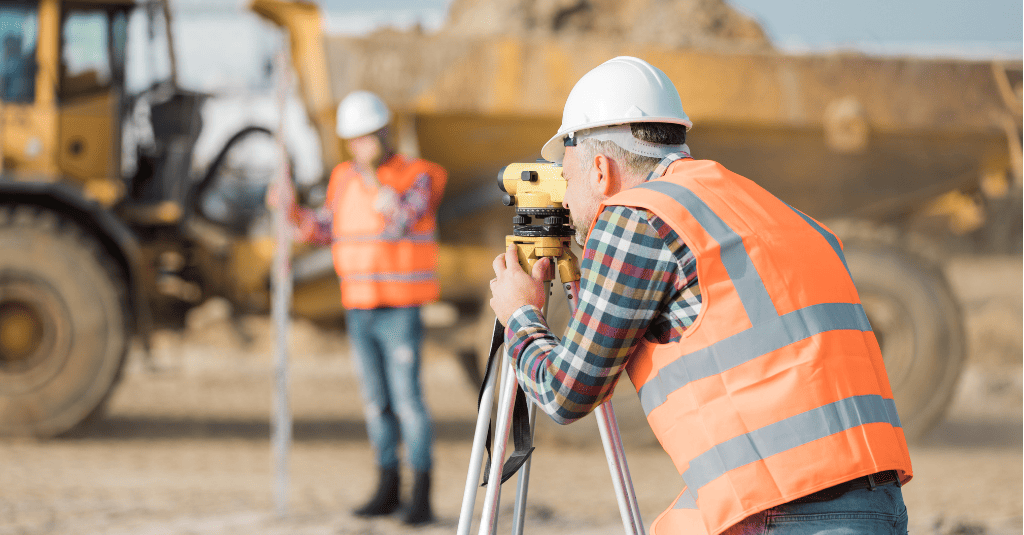
Defensa
Informática COTS (Componente sacado del estante) esencial para la misión que proporciona procesamiento de alta potencia y fiabilidad en entornos operacionales.
Seguridad Pública
Ambulancia, Cuerpo de bomberos, Policía
Servicios Públicos
Lecturas e instalación de medidores inteligentes, seguridad in situ, gestión de activos para servicios públicos, gestión del personal para servicios públicos, lecturas e instalación de medidores inteligentes
Transporte y Logística
Gestión ferroviaria, gestión aeroportuaria, gestión portuaria, gestión de flota de envío a larga distancia, manejo de materiales de almacén
Petróleo y Gas
Asistencia a distancia, Gestión de activos, Análisis de datos de campo, Seguridad en el lugar de trabajo
Manufactura industrial
Programación industrial y control robótico, gestión de instalaciones, cumplimiento e inspecciones, gestión del personal, gestión de inventario y almacén, automatización de fábrica y monitoreo de planta, gestión de activos empresariales y sistemas de gestión de mantenimiento computarizado
Sector Automotriz
Las notebooks y tabletas robustas permiten un mejor desarrollo del sector aumotriz
Recursos naturales
Aplicaciones para Minería, Aplicaciones Rorestales y Construcción
Since the pandemic, many employees can work from home. Those who work with machines or deliver frontline services, like the utility and manufacturing sectors, usually cannot. The United States employs a whopping 50 million frontline workers, and the pandemic is far from over. A question that is front and center in many industries is: How do we keep employees safe while still getting work done?
To do so, frontline industries need to transform and adopt ways of working, which include:
The post-pandemic landscape will have workers as a vital resource with a low-touch approach, complemented with data insights and automation. Technology, through digital transformation, will help deliver the correct data to the worker. This, in turn, enables the work will to be more innovative for increased productivity.
The talk of digital transformation has been growing louder and more intense over the last few years. Work in frontline sectors has already been making progress toward more efficient models. But the framework had been patchy, and adoption, scattershot, or stalled.
It was the COVID-19 pandemic that gave industries a much-needed kick in the seat of the pants. It also accelerated the adoption of advanced technologies. A McKinsey survey of executives found that the pandemic expedited the global adoption of digital transformation by three years.
What technologies do industries, especially those at the frontlines, need to embrace to evolve to a more efficient data-driven approach? We outline a few that work together to shape the frontline post-COVID landscape of tomorrow.
As a post-pandemic workplace trend, artificial intelligence (AI) and a version of machine learning (ML) help enterprises use talent more efficiently. Users train ML models on historical data to detect and learn patterns. When used on incoming data, these systems can detect and flag anomalies in the machine or other behaviors to proactively solve problems.
New information also feeds into the cloud-based model. This enables the program to add to its bank of real-life data points and use it for future troubleshooting. Expect AI implementation to increase in the post-COVID landscape. A 2022 IBM research report found that global AI adoption — across all sectors, not just frontline ones — grew to 35 percent.
If the post-COVID landscape will need minimal human supervision and facilitate remote overview, we need machines to communicate if there’s a problem and run smoothly if there’s not. The Internet of Things (IoT) executes this function by enabling sensor-embedded equipment to relay live information about their health.
Users can program these data points to be as frequent as needed. By analyzing this information, workers can rest assured that all systems are functioning smoothly and intervene only as and when necessary. IoT complemented by visualization platforms will help workers keep a remote eye on processes across multiple portfolios. Rugged devices like those from Getac will help access data in various locations.
A digital twin is a model that captures all information about machines and processes. It is akin to a virtual replica of the real-life equivalent. Using a digital twin makes frontline work more efficient. It allows companies to simulate what-if scenarios: what if the part from vendor A does not reach us on time? What if our workforce is reduced by 10 percent next week?
Modeling future what-if scenarios helps relevant stakeholders make data-driven decisions. Doing so would lessen the guesswork and waste, and workers could do their jobs more efficiently.
Edge computing occurs when data processing happens close to the data source and therefore offers lower latency of operations. Instead of users routing data to the cloud, on-prem capabilities help crunch the volumes of information coming from various data sources, including machines. Some decisions cannot wait until tomorrow or the next hour; they need to be made now. In such instances, edge computing with decreased latency is critical.
Frontline workers are mobile and on the go. They need to access data wherever they are to make informed decisions.
Augmented reality (AR) delivers such data in a manner that is visual and easy to understand. AR overlays digital information overviews of the live situation on the ground.
Using AR, workers can compare and contrast what an ideal situation should look like versus what it looks like on the ground. This technology can help them fix problems more efficiently, occasionally leaning on remote help.
AR solutions on rugged mobile devices like those from Getac help on several fronts. The first is to access real-time information on the go. The second is acting on insights from advanced technologies such as IoT and AI.
An increased focus on employee safety and talent will increasingly mean that collaborative robots, working alongside employees, will do the routine grunt work. In contrast, humans focus on higher-order tasks that they do best. Expect collaborative robots to take on dull, dangerous, and repetitive tasks so the workplace is safer and enterprises can strategically use talent.
It might be cliche, but technology is no magic bullet. It will take people, process, and technology to make systems work together and realize new efficiencies. A key post-pandemic workplace trend was the sharp wake-up call that urged the industry to review existing processes and recalibrate. While we cannot forecast the future, adopting a technology-driven approach will make operations more resilient to shocks in the future.
Mike McMahon is the President of Getac North America. Mike is experienced in the rugged OEM computing business on both end user and channel side. His unique perspective on rugged technology spans Enterprise, Public Safety, and Federal markets.