The global warehousing market continues to see the pressure of higher demand and quicker turnaround. Staying competitive requires increased efficiency for logistics and operations. One of the most substantial cost savings opportunities in production is efficiently moving materials through a manufacturing site or warehouse. The discipline of material handling combines the equipment needed with the warehouse management system (WMS) to ensure seamless material movement for increased operating efficiency.
The movement of significant components through a facility has its share of challenges. Among these are:
- Space limitations due to warehousing cost
- Real-time tracking and inventory management
- Equipment wear and maintenance needs
- Technology integration, updating, and security
- Worker safety as sites pursue a higher throughput
A truly optimised warehouse layout ensures the best flow of materials, organised from fast to slow-moving parts, to ensure rapid material flow and order fulfilment. Inaccurate inventory can be costly, but the ability to track and update your inventory in real-time ensures warehouse operatives swiftly convert inventory to goods sold while managing the inventory carrying cost. Significantly, good material handling practises improve worker safety.
Implementing efficient material handling practises addresses the challenges faced in manufacturing and warehouse applications. Fortunately, commercially available solutions today can optimise material handling efficiency, capital durability, inventory cost, and worker safety. One such technology is using demountable rugged computing devices fitted to the material handling equipment.
Understanding Material Handling
Material handling is a critical component of warehouse operations, encompassing the movement, storage, protection, and control of materials throughout the supply chain. It involves the use of various equipment and techniques to ensure the efficient and safe handling of goods, from receiving and storage to shipping and delivery. Effective material handling is essential for maintaining a smooth and productive warehouse operation, reducing costs, and improving customer satisfaction.
In warehousing and material handling, the goal is to streamline the material handling process to ensure that goods are moved efficiently and safely. This process involves using the right material handling equipment, such as pallet jacks, conveyor systems, and automated storage solutions, to facilitate the movement and storage of materials. Proper material handling not only enhances warehouse operations but also plays a crucial role in the overall supply chain, ensuring that products are delivered to customers on time and in good condition.
How Technology and Digitalisation are Shaping the Industry
Led by AI and smart manufacturing, industrial manufacturing, operations, and supply chain are transforming like never before. Sensors, automated systems, and data collection from the inventory operations provide a wealth of data that software analyses to influence process changes.
An example of this is Dexory's digital twin used for warehouse management. The solution collects data from physical warehouse assets and builds a CAD or twin model that engineers can manipulate to optimise inventory and efficiency. The real-world data is digitised, enabling automated analysis.
Warehouse material handling equipment plays a crucial role in enhancing operational efficiency by effectively moving materials within the warehouse.
Another application for technology-driven enhancement to material handling is BotsAndUs's AI autonomous robot. Like the digital twin, the robot collects and analyses data in real time, reacting much faster to changes in conditions to continually optimise performance and efficiency while minimising the potential for human error.
Just as digital twins aim to reduce the transition time between physical and digital worlds to improve efficiency and speed up reaction time, vehicle mounts aim to shorten the physical distance between the operator and technology. In addition, these tools deliver additional operational improvements through decentralising the digital interface.
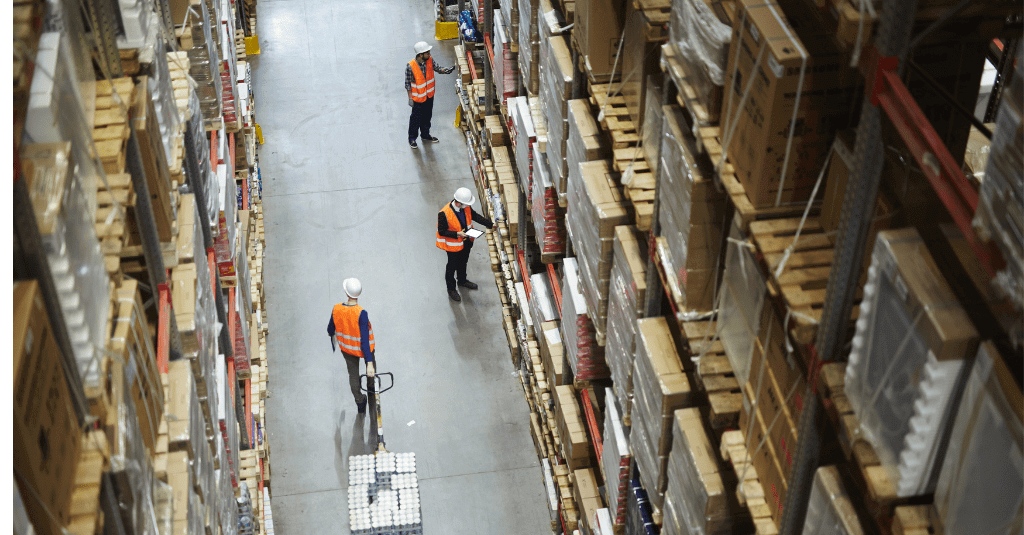
Material handling equipment requires a warehouse management system to ensure seamless material movement for increased operating efficiency.
The Importance of Material Handling Solutions
Ensuring your workforce has access to the latest demountable computer technology ensures that they have real-time access, increased efficiency, and minimal downtime. Mounting solution options give the flexibility to be installed on multiple other material handling systems and equipment.
Two types of mounting solutions to consider are docking stations and cradles. The primary difference is that cradles are specific to the device and do not replicate the ports, while the docking station provides port replication for the computing devices.
Vehicle docks or cradles provide a safe and reliable solution for mounting rugged computing devices while affording the operator hands-free data access. These features are critical in many applications, including high-intensity material handling warehouse operations, where an unsecured tablet or laptop can launch across the site, leading to injury. In material handling, many applications could leverage vehicle docks or cradles, such as:
- Forklifts that travel between storage locations to pick the material using barcodes or RFID scanning
- Specialised function machinery like cranes are hoists that require human operation or oversight to transport material safely from a distance
- Vehicles that move material to and from the warehouse or plant to provide the driver with timing, location, and schedule changes quickly
Considerations for Optimal Material Handling Equipment
While the mounting locations are flexible, interfering with the handling equipment is a legitimate concern. When designing a mount location, engineers should consider the operator's way of working and likely movement patterns. Is the device mount within the worker's reach but out of their normal range of motion or line of sight when performing tasks? Also, consider if the device mount creates potential blind spots. During regular daily operation, what areas may become hidden with the addition of mounted technology devices?
Ease of access and how the operator interacts with the device should be considered when considering what mount type to use and where it will be mounted. Workers will use the onboard technology multiple times throughout the workday. Is it mounted in a location where access does not impede the user's typical daily performance?
Another consideration is mount durability. For example, is the application subject to excessive vibration that could dislodge the device from the holder? In addition, shock or vibration fatigue, extreme temperature cycles, and dusty environments could all damage the device. As a result, mounting design should consider likely application environments to guard against damage to the device or connections.
Optimising Warehouse Layout for Efficient Material Handling
A well-designed warehouse layout is crucial for efficient material handling. The layout should be optimised to minimise travel distances, reduce congestion, and improve accessibility. This condition can be achieved by:
- Designating specific areas for receiving, storage, and shipping: Clearly defined zones help streamline the material handling process, ensuring that materials are moved efficiently from one area to another.
- Implementing a logical and consistent labelling system: A standardised labelling system helps workers quickly locate and identify materials, reducing the time spent searching for items.
- Utilising vertical space with shelving and racking systems: Maximising vertical space helps improve space utilisation, allowing for more efficient storage of materials.
- Implementing a warehouse management system (WMS) to track inventory and optimise storage: A WMS provides real-time visibility into inventory levels and locations, helping to optimise storage and retrieval processes.
By optimising the warehouse layout, businesses can improve material handling efficiency, reduce labour costs, and increase productivity. An efficient layout enhances the flow of materials and contributes to a safer and more organised work environment.
Benefits of Using Vehicle Docks or Cradles in Worker Safety and Productivity
The most impactful benefit vehicle docks or cradles provide for logistics performance is increased operating efficiency. When moving the technology closer to the user, retrieval systems such as demountable rugged computing solutions allow operators to scan inventory codes or record vehicle performance information. Quicker scans mean increased material processing and increasing throughput per hour worked. In addition, vehicle docks allow drivers to remain in their handling vehicles, with controlled access to the rugged device only when stationary, which reduces the likelihood of a safety incident.
- Manages reduction of vibrations and shocks to the demountable device
- Extends port replication
- Increased safety and security with the ability to lock the device in place
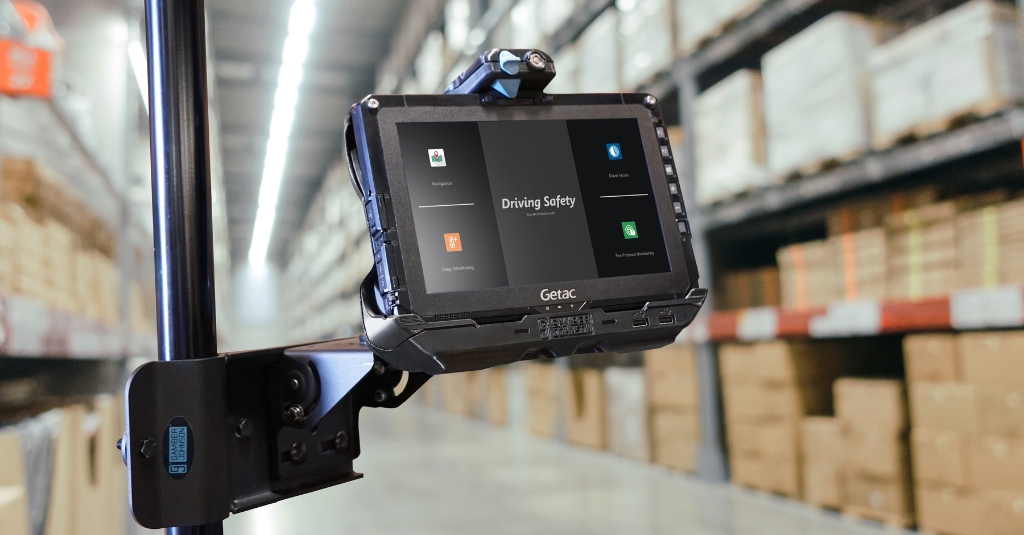
Getac UX10 rugged tablet with Gamber-Johnson tube mount
Benefits of Optimised Material Handling Processes
Optimised material handling processes can bring numerous benefits to a warehouse operation, including:
- Improved efficiency and productivity: Streamlined material handling processes reduce the time and effort required to move materials, increasing throughput and productivity.
- Reduced labour costs and improved employee safety: Efficient material handling reduces the physical strain on workers, lowering the risk of injuries and associated labour costs.
- Increased accuracy and reduced errors: Automated material handling systems and accurate inventory tracking help minimise mistakes, ensuring that suitable materials are delivered to the correct locations.
- Enhanced customer satisfaction and loyalty: Efficient material handling processes ensure timely and accurate order fulfilment, leading to higher customer satisfaction and loyalty
- Improved inventory management and reduced stockouts: Optimised material handling processes help maintain accurate inventory levels, reducing the risk of stockouts and overstock situations.
- Increased competitiveness and market share: By improving operational efficiency and customer satisfaction, businesses can gain a competitive edge and increase their market share.
By implementing optimised material handling processes, businesses can gain a competitive edge, improve customer satisfaction, and increase profitability. These benefits highlight the importance of investing in efficient material handling solutions and practises.
Implementing a Warehouse Management System (WMS)
A warehouse management system (WMS) is a software solution that helps businesses manage and optimise their operations. A WMS can:
- Track inventory levels and locations: Real-time inventory tracking helps ensure accurate stock levels and reduces the risk of stockouts and overstock situations.
- Optimise storage and retrieval processes: A WMS helps optimise the placement of materials within the warehouse, reducing travel distances and improving retrieval times.
- Improve picking and packing efficiency: A WMS helps reduce errors and increase order fulfilment speed by streamlining the picking and packing processes.
- Enhance shipping and delivery processes: A WMS provides real-time visibility into shipping and delivery status, helping to ensure timely and accurate deliveries.
- Provide real-time visibility and reporting: A WMS offers comprehensive reporting and analytics, providing valuable insights into warehouse operations and helping identify improvement areas.
By implementing a WMS, businesses can improve material handling efficiency, reduce errors, and increase productivity. A WMS is a valuable tool for optimising warehouse operations and ensuring that materials are handled efficiently and accurately.
Best Practises for Material Handling
To ensure efficient and safe material handling, businesses should follow best practises, including:
- Providing regular training and education to employees: Ongoing training ensures that employees are knowledgeable about proper material handling techniques and safety protocols.
- Implementing a safety programme and enforcing safety protocols: A comprehensive safety programme helps prevent accidents and injuries, ensuring a safe work environment.
- Conducting regular maintenance and equipment inspections: Regular maintenance and inspections help ensure that material handling equipment is in good working condition, reducing the risk of breakdowns and accidents.
- Utilising proper equipment and techniques for handling materials: Using the right equipment and techniques helps ensure that materials are handled safely and efficiently.
- Implementing a quality control programme to ensure accuracy and quality: A quality control programme helps maintain high standards of precision and quality, reducing errors and improving customer satisfaction.
By following best practises, businesses can ensure efficient and safe material handling, reduce errors, and improve customer satisfaction. These practises are essential for maintaining a productive and safe warehouse operation.
Getac and Gamber-Johnson Solutions for Material Handling
A rugged device and mounting solution that can withstand the harsh environment of a warehouse or manufacturing plant are essential to incorporating digital solutions to realise the efficiency and safety gains from optimised material handling processes. Getac offers rugged tablets like the Windows OS F110 and Android OS ZX10 to suit any warehousing application. Paired with the Getac Driving Safety Utility software, worker safety is ensured whilst on the move.
Gamber-Johnson offers material handling mounts for lift vehicles, peripheral applications, and versatile uses that can withstand challenging environments and situations in the warehouse. These solutions reduce installation time while improving safety and ergonomics. Gamber-Johnson's development on mount placement maintains roll cage and safety guard integrity while providing a superior device location for the more rugged, reliable, and responsive adaptation into the warehouse material handling workspace. Mounts are made from high-strength aluminium to withstand indoor or outdoor elements.
Gamber-Johnson's material handling system mounts offer application flexibility and complete mounting solutions for all Getac devices. Gamber-Johnson can support the mount, docking station, accessory mount (keyboard, printer, additional monitor), and a power supply for those long shifts to optimise efficiencies. The optimal location to attach a device may differ for each company and each lift truck within an organisation. Considering how materials and people move throughout the facility will help select the best mounting solution.
Visit Getac's warehousing engineered systems & materials page to learn more about rugged technology solutions delivering significant benefits to plant and warehouse operations.
Frequently Asked Questions
What is material handling?
Material handling is the movement, transportation, control, storage and retrieval systems and distribution of materials, objects, and goods as they move through the warehouse or plant.
What are the different types of material handling equipment?
Equipment can be industrial trucks, pallet trucks, storage equipment, manual handling equipment trucks, or specialised equipment for transporting goods.
What are some of the issues and challenges workers in this industry encounter?
High handling costs through manual loading, inventory tracking, space limitations, worker safety, and equipment wear.
How can materials handling equipment increase the effective capacity of warehouses?
Efficient use space utilisation of assets, improved worker safety, and streamlined transport loads, containers, and bulk materials management.