How Digital Transformation is Reshaping Warehouse Inventory Management
Inventory management is a critical aspect of warehousing that involves overseeing the movement and storage of products in a warehouse. It ensures businesses maintain adequate stock levels to meet customer demands while minimizing carrying costs. Effective inventory management requires accurate tracking, timely replenishment, and space utilization.
In a perfect world, warehouses would not need to exist. Companies would know precisely how much a customer wants, needs, and when they need it. As it stands today, warehouses are critical for ensuring that products move efficiently from manufacturers to retailers and ultimately to consumers.
The digital transformation of warehouses is revolutionizing this landscape. By integrating advanced warehouse inventory systems, companies can now predict customer needs more accurately, making the concept of a 'perfect world' more achievable. These systems use data analytics and machine learning to forecast demand, optimize stock levels, and streamline the flow of goods through the supply chain, marking a significant shift in how warehouses operate.
However, the disruptions within the supply chain over the past few years have uncovered many of the inefficiencies and opportunities within warehousing. Our modern-day warehouses still manage inventory using manual processes, paper, and spreadsheets, with industry experts estimating ~80% of warehouses lack automation.
The labor scarcity and lower technology costs make warehouse investments more attractive than they were in the past. Companies see the value of investing in digital transformation technology within the warehouse to build a more resilient and efficient supply chain. This article aims to provide an accessible overview of warehouse inventory management, highlighting the importance of digital transformation for improved efficiency and adaptability in this vital sector.
The Role of Warehousing Within the Supply Chain
Warehouses play a pivotal role in the modern supply chain, acting as the backbone for efficient inventory control, management, storage, and distribution of goods.
An integral part of this evolution is the implementation of data warehouse inventory management systems. These sophisticated systems collect, store, and analyze vast amounts of data, providing real-time insights into inventory levels, product movement, and supply chain dynamics. This data-driven approach enhances decision-making and helps warehouses respond swiftly to market changes, enhancing their role in the supply chain.
Warehouses contribute significantly to the overall success of a business in the following ways:

Centralized storage: Warehouses provide a centralized location for storing goods and products, allowing businesses to manage their inventory levels efficiently.

Smooth flow of goods: Warehouses play a crucial role in ensuring a smooth flow of goods through the supply chain by acting as intermediaries between manufacturers, suppliers, and end customers. They facilitate the movement of goods from production to distribution and returns processing.

Inventory management: Warehouses enable businesses to maintain adequate stock levels, ensuring they can meet customer demand without overstocking or running out of products.

Economies of scale: By consolidating storage and distribution activities in a single location, warehouses help businesses achieve economies of scale, reducing overall costs and increasing operational efficiency.

Value-added services: Warehouses often provide additional services such as packaging, labeling, and quality control, further streamlining the supply chain process.

Risk management: Warehouses help minimize risks associated with theft, damage, and spoilage by providing secure, controlled environments for storing goods. They also help businesses manage fluctuations in demand and supply, acting as a buffer during times of excess or shortage.

Just-in-time delivery: Warehouses support just-in-time (JIT) delivery models by ensuring that goods are readily available for shipment when needed, reducing lead times and improving customer satisfaction.
Warehouses are pivotal in today's modern supply chain, serving as the backbone for efficient product distribution. These storage facilities facilitate the movement of goods from manufacturers to end consumers, ensuring timely deliveries and enhanced customer satisfaction. Effective inventory management in warehouses is essential to capitalize on their potential.
What is Warehouse Inventory Management?
Inventory management, a vital aspect of inventory control and warehouse automation, is a critical aspect of warehousing that involves overseeing the movement and storage of products in a warehouse. It ensures businesses maintain adequate stock levels to meet customer demands while minimizing carrying costs. Effective inventory management requires accurate tracking, timely replenishment, and space utilization.
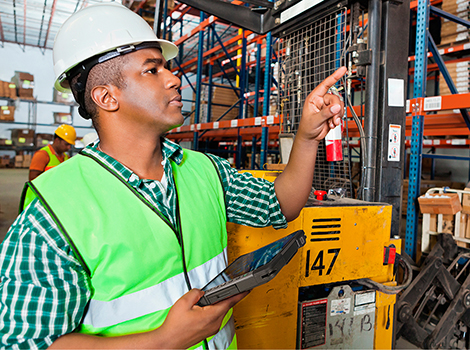
Requirements for Proper Warehouse Inventory Management

- Accurate and real-time tracking of inventory levels
- Timely replenishment to avoid stockouts and overstocking
- Effective space utilization to optimize warehouse capacity
- Streamlined and efficient warehouse processes to ensure inventory accuracy
Best Practices for Warehouse Inventory Management

- Use technology solutions like Warehouse Management Systems (WMS) for real-time visibility and enhanced decision-making capabilities.
- Adopt methods and procedures such as lean or 5S for efficient warehouse processes.
- Implement a regular cycle count schedule to maintain inventory accuracy.
- Prioritize items using ABC analysis to allocate resources effectively.
- Develop a Sales and Operations Planning (SOP) process to align inventory management with business objectives.
Benefits of Good Warehouse Inventory Management
Modern warehouse inventory control systems are at the heart of these benefits. By automating key inventory management processes, these systems reduce manual errors, enhance stock visibility, and facilitate more effective space utilization. As a result, warehouses can achieve greater operational efficiency and accuracy, directly contributing to improved business performance.

- Improved productivity: Streamlined picking and packing processes lead to increased efficiency and faster order fulfillment.
- Reduced labor costs: Automation and optimized workflows reduce the need for manual labor, lowering operational expenses.
- Accurate forecasting: Data-driven insights enable precise demand predictions, facilitating better planning and resource allocation.
- Lean inventory management: Enhanced visibility and control over stock levels simplify the implementation of lean inventory practices, minimizing waste and excess inventory.
- Increased accuracy: Real-time inventory tracking and order fulfillment ensure orders are processed accurately, reducing costly returns and exchanges.
- Better customer service: Promptly meeting customer demand leads to improved satisfaction and loyalty.
Consequences of Poor Warehouse Inventory Management
The consequences of not utilizing advanced warehouse inventory systems are becoming increasingly apparent. These systems, which are a fundamental aspect of digital transformation in warehouses, offer streamlined and automated solutions to manage inventory more effectively. In their absence, warehouses face challenges like mismanaged stock, inefficient use of resources, and delayed responses to market demands.

- Stock shortages lead to lost sales and dissatisfied customers
- Overstocking results in increased carrying costs and reduced profitability
- Inaccurate inventory tracking causes discrepancies and errors in order fulfillment
- Wasted warehouse space due to inefficient inventory management
Technology vs. Manual Processes

- Technology solutions like warehouse management systems, automated data collection, and barcoding offer real-time visibility and enhanced decision-making capabilities.
- Manual processes are inefficient and prone to errors, leading to inaccurate inventory tracking and order fulfillment.
What is an ABC Analysis in warehouse inventory management?

- Prioritizes items based on their value to allocate resources effectively
- Classifies items into three categories: A (high-value items), B (medium-value items), and C (low-value items)
What is a Sales and Operations Planning (SOP)?

- Aligns warehouse inventory management with business objectives
- Develops a demand, supply, and inventory plan to ensure optimal operations and profitability.
By implementing mobile warehouse inventory management technology solutions, best practices, and effective processes, businesses can streamline warehouse inventory management to achieve optimal efficiency and profitability while meeting customer demands.
This adoption of mobile and digital technologies is a crucial element of the broader warehouse digital transformation. Embracing these innovative tools not only refines warehouse inventory management but also reshapes the entire warehousing experience. This transformation leads to more agile, responsive, and efficient warehouse operations, crucial for businesses to thrive in today's fast-paced market environment.
Getac’s Rugged Tablets are Digital China’s Solution to Warehouse Automation
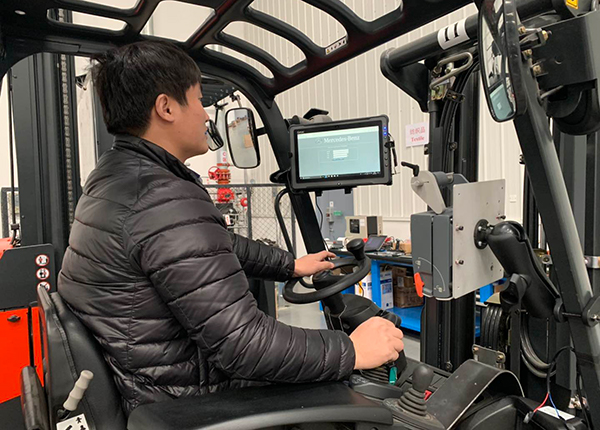
The Need for Digital Transformation in Warehouse Inventory Management
In the modern retail landscape, warehouses face numerous challenges associated with traditional manual processes, leading to inefficiencies, errors, and increased operational costs. Some of these challenges include:
- Industrial Safety: A people-oriented organizational culture prioritizes safety as a foundational aspect of warehouse operations. By implementing digital solutions, businesses can enhance safety measures and foster a safety-first mindset among employees to reduce common warehouse injuries.
- Maintenance and Inspection: Ensuring equipment and tools operate optimally prevents operational and business disruptions. Digital transformation, through the implementation of warehouse mobile solutions, enables better tracking of maintenance periods and quality control, mitigating potential issues.
- Storage and Supply Chain: Efficient storage and supply chain management are at the heart of successful warehouse operations. Adopting digital technologies allows for improved space utilization, streamlined processes, and the ability to adapt to seasonal demand fluctuations.
- Staff and Material Handling: Effective staff management and material handling practices can drive cost-effective measures within warehouse environments. Digital transformation facilitates better labor cost management and optimizes the use of material handling equipment.
Benefits of Mobility Solutions in Warehouse Operations
Mobility solutions, including warehouse mobility solutions, are vital in streamlining warehouse operations, tracking real-time inventory, and improving team communication for effective warehouse inventory tracking. The following benefits of implementing mobility solutions demonstrate their significance in modern warehousing:
- Increased accuracy: Digital systems reduce errors in warehouse inventory management and order processing, ensuring accurate stock information and timely deliveries.
- Improved productivity: Mobility solutions enable workers to access real-time data and task instructions, reducing time spent on manual data entry and allowing them to focus on more value-added activities.
- Enhanced safety: By leveraging technology, such as wearables and automated equipment, warehouses can minimize the risk of accidents and create safer work environments.
- Cost savings: Streamlined processes and improved efficiency through digital transformation can lead to significant cost savings in labor, inventory management, and overall operational expenses.
- Less walking: It's no surprise that warehouse employees walk a lot, with some saying up to 12 miles daily. When mobile solutions integrate with a warehouse management system that includes digital picking, they eliminate the need for warehouse employees to walk back and forth, enhancing inventory management with digital picking.
Related solutions
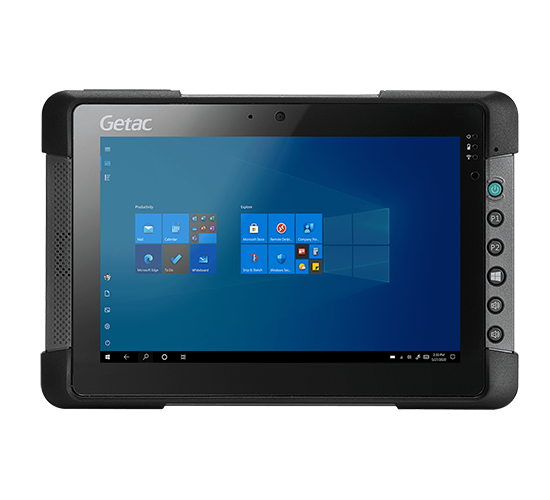
T800
Tablets | Fully Rugged | 8-Inch | Windows
The T800 has an 8.1-inch screen, a thin, ergonomic design, reliable battery life, and no-compromise rugged features.
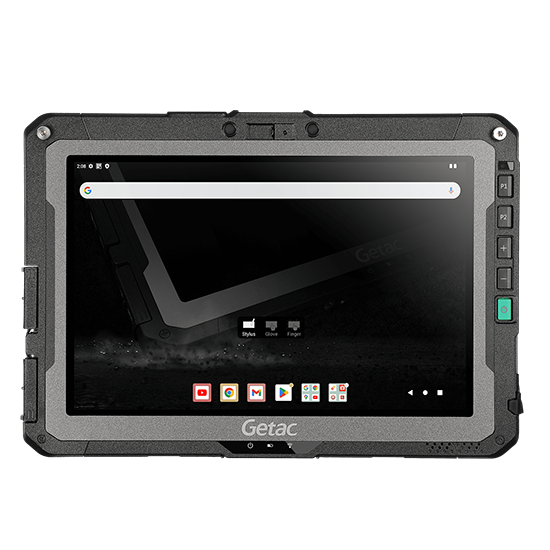
ZX10
Tablets | Fully Rugged | 10-Inch | Android
The ZX10 10-inch Android tablet offers an exceptional solution combining intuitive operation and power efficiency with a slim versatile profile.
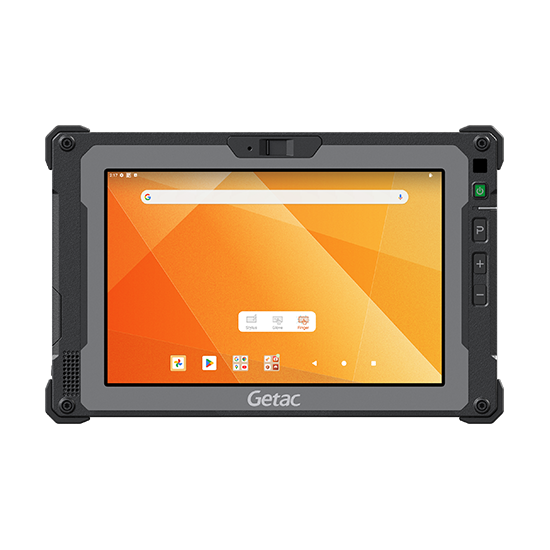
ZX80
Tablets | Fully Rugged | 8-Inch | Android
The ZX80 8” fully rugged Android tablet is a built-for-AI powerhouse. The ZX80 puts real-time analytics, facilities management, and UAV piloting in the palm of your hands, and features extreme tolerances and a long battery life in a sleek lightweight package.
Technology Solutions for Digital Transformation in Warehousing
To stay competitive in the fast-paced retail landscape, warehouses must embrace digital transformation by adopting innovative technology solutions. This section will focus on key areas of technological advancement in warehouses.
Robotics and Automation Solutions for Warehouses
Integrating robotics and automation solutions is essential for modern warehouses seeking to optimize operations and improve efficiency. Some of the leading technologies in this domain include:
- Autonomous Mobile Robots (AMRs): AMRs are advanced robotic systems that can navigate through warehouses autonomously, performing tasks such as picking, transporting, and sorting items.
- Automated Guided Vehicles (AGVs): AGVs are self-guided vehicles that move materials and goods within a warehouse, follow predefined routes, and reduce manual labor in material handling processes.
- Automated Storage and Retrieval Systems (AS/RS): AS/RS are computer-controlled systems designed to automatically store and retrieve goods in warehouses, streamlining warehouse inventory management and optimizing storage space utilization.
Choosing the right automated warehouse management solution depends on many factors, including budget, warehouse layout, size, products, etc. Automated solutions continue to improve, providing businesses with greater inventory control and integration with warehouse inventory management systems.
Key Software Solutions for Modern Warehouses
Warehouse management software includes digital warehouse management systems, inventory management software with digital picking features, yard management systems, dock scheduling software, and more. By incorporating advanced inventory management software, companies ensure real-time tracking of goods, enabling them to maintain accurate stock levels and minimize risks associated with stockouts or overstocking. Furthermore, other warehouse management software integrates with accounting systems to ensure prompt payments and reconciliation.
Other warehouse management software integrates with various technology to automate critical processes such as order picking, packing, and shipping, which results in improved order fulfillment and operational efficiency. These software solutions also offer valuable insights into warehouse layout optimization, allowing businesses to maximize space utilization and enhance overall productivity.
Common Warehouse Management Software
- Warehouse Management System (WMS): A WMS, especially when integrated with digital picking techniques, optimizes warehouse operations, including inventory tracking, order processing, and workforce management, showcasing the importance of warehouse management with digital picking.
- Enterprise Resource Planning (ERP): ERP systems integrate different business functions, such as finance, sales, and procurement, into a single platform. For warehouses, an ERP system can connect inventory management with other business processes, enabling better decision-making and resource allocation.
- Inventory Management System (IMS): An IMS focuses on maintaining accurate inventory levels, tracking stock movement, and generating alerts when stock levels are too high or low. This system helps warehouses avoid overstocking or stockouts, ensuring efficient warehouse inventory management.
- Warehouse Execution System (WES): A WES combines the functionalities of a WMS and a Warehouse Control System (WCS) to coordinate and optimize the execution of warehouse tasks. It manages manual and automated processes, such as material handling equipment and robotics, to enhance overall warehouse efficiency.
- Yard Management Systems (YMS): A YMS is a specialized software solution designed to streamline inventory control and optimize the flow of goods within a warehouse's yard, effectively complementing inventory management systems.
By providing real-time visibility of inbound and outbound shipments, YMS enhances inventory control, ensuring accurate stock levels and facilitating efficient communication between various stakeholders. As an integral component of modern inventory management systems, YMS empowers businesses with data-driven insights, enabling them to make informed decisions and boost operational efficiency in a competitive market landscape.
Related solutions
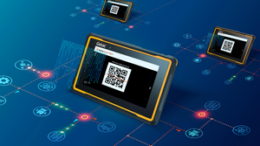
Getac deployXpress®
Software | Android
This cloud-based solution streamlines the deployment, configuration, provisioning, and over-the-air updating of Getac Android devices.
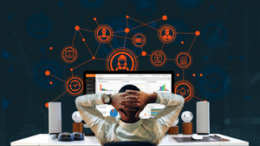
Device Monitoring System
Software | Windows
GDMS tracks and monitors deployed devices, spotting potential device issues, before they impact on your field-based workforce.
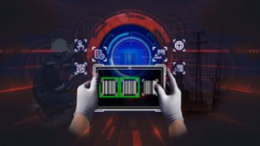
Getac KeyWedge Barcode Reader Utility
Software | Windows
Scan barcode data into your application with the devices in-built rear camera. No hardware. No upgrades. No SDK integration required.
Popular Mobile Devices Used in Warehousing
Mobile solutions are becoming more prevalent in modern warehouses. Companies are leveraging technology like smartphones and other mobile devices. Since most people are familiar with this technology, it speeds up training.
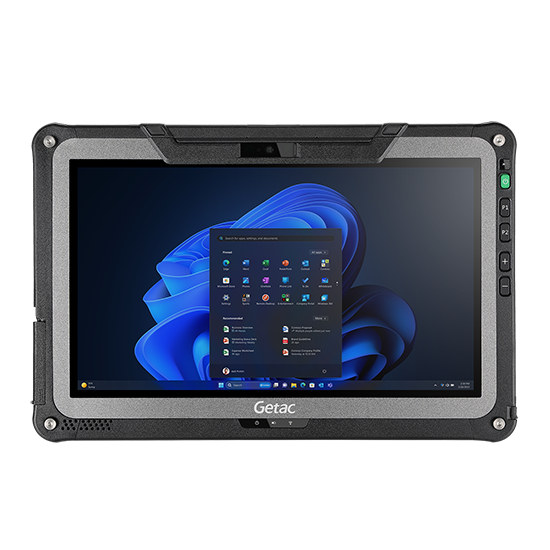
F110
Tablets | Fully Rugged | 11.6-Inch | Windows
The F110 was named the Best Rugged Tablet in 2021 by ZDNet and in 2023 by TechRadar. It has a slim form factor and an 11.6-inch FHD screen.
Mobile solutions, as part of digital warehouse management strategies, are becoming more prevalent in modern warehouses. Companies are leveraging technology like smartphones and other mobile devices. Since most people are familiar with this technology, it speeds up training.
- Tablets: Rugged tablets provide warehouse workers with a portable, durable solution for accessing crucial information, such as inventory data and task instructions. Rugged tablets enable efficient monitoring and control of IoT devices, facilitating real-time data collection and analysis. By utilizing rugged tablets, warehouse engineers can optimize IoT device management, enhance maintenance practices, and streamline programming processes, ultimately improving operational efficiency and productivity.
- Smartphones: Smartphones equipped with dedicated warehouse management apps enable warehouse workers to communicate seamlessly, track inventory, and manage tasks on the go.
- Smart devices: Wearable devices offer hands-free access to information, enhancing worker productivity and safety.
- Mobile workstations: Built to withstand harsh warehouse environments, mobile workstations allow warehouse employees to access data and manage tasks without a desk.
Getac's inventory and warehouse management solution integrates seamlessly with leading inventory management, ERP, and WMS software. Getac's rugged devices have both the computing power and ruggedness required for you to work at ease, providing an ideal platform for inventory and warehouse management.
Choosing the Right Mobility Solution for Your Business
Selecting the appropriate mobility solution for your warehouse is a critical decision that can significantly impact your business's efficiency and productivity. To make an informed choice, it's essential to consider various factors and perform a cost-benefit analysis. This section will discuss the key aspects to evaluate when choosing a mobility solution for a warehouse inventory management system.
Factors to Consider When Choosing a Mobility Solution

Compatibility: Ensure seamless integration with your existing warehouse management system (WMS), enterprise resource planning (ERP), and other software platforms.

Purpose and Application: Assess the specific warehouse functions where rugged tablets will be utilized, such as on forklifts for inventory tracking, streamlining the picking and packing process, aiding dispatchers in coordinating shipments, or facilitating crane operators in material handling. Select hardware specifically designed for these environments to maximize efficiency and effectiveness.

Scalability: Opt for a solution that can adapt to your business's growth, allowing the addition of more devices or features as your needs evolve.

Ease of Use: Choose user-friendly devices and applications to minimize the learning curve for warehouse staff, promoting quick adoption and efficient utilization.

Durability: Invest in rugged and reliable devices capable of withstanding harsh warehouse conditions, including dust, moisture, and temperature fluctuations, to ensure long-lasting performance.

Security: Evaluate the data security measures provided by the mobility solution, such as encryption, secure connectivity, and data backup, to safeguard sensitive business information.
Cost vs. Benefit Analysis of Implementing a Mobility Solution
A thorough cost-benefit analysis can help determine the potential return on investment (ROI) for implementing a mobility solution in your warehouse. Key aspects to consider include:

Initial investment: Calculate the upfront costs of purchasing devices, software licenses, and any necessary integration services.

Ongoing expenses: Factor in the recurring costs, such as maintenance, software updates, and support services, to determine the total cost of ownership (TCO) of the solution.

Productivity gains: Estimate the expected increase in worker productivity and efficiency from implementing the mobility solution.

Cost savings: Analyze potential cost savings in labor, inventory management, and error reduction, which can offset the initial investment and ongoing expenses.
By carefully considering these factors and conducting a comprehensive cost-benefit analysis, you can make an informed decision about the proper mobility solution for your business, ultimately enhancing efficiency and staying competitive in the retail industry.
Getac's Mobility Solution: Spearheading Digital Transformation in Warehouse Inventory Management
With the right technology solutions, warehouses can simplify inventory management. Digital transformation is critical for the material handling industry to stay competitive. Technology solutions, such as robotics and automation, IoT, and mobility solutions, offer significant benefits, from productivity gains to cost savings and enhanced safety.
By adopting these solutions, warehouses can streamline operations, optimize inventory management, and improve worker satisfaction.
Getac's rugged devices are an ideal inventory and warehouse management platform, providing efficient and seamless integration with leading software platforms and proprietary software like Getac driving safety utility
If you want to start your digital transformation journey with mobility solutions, contact Getac for further information on modernizing your warehouse operations.
FAQ
What is the purpose of a warehouse?
A warehouse is a large commercial building for storing, organizing, and distributing goods and products. Warehouses are strategically located near transportation hubs, such as highways, ports, and railways, to facilitate efficient distribution of goods. This positioning enables businesses to minimize transportation costs and optimize response times for customer demands. This section will discuss the common characteristics and types of warehouses catering to various business needs.
What are the common characteristics of warehouses?
Warehouses come in various sizes depending on the business's needs. Small and medium-sized warehouses are typically used for local storage, while large warehouses and distribution centers serve a broader geographical area. The size of a warehouse is determined by various factors such as the volume of goods to be stored, the frequency of goods movement, and the type of products. Small warehouses may range from 5,000 to 20,000 square feet, mid-size warehouses from 20,000 to 100,000 square feet, and large warehouses over 1,000,000 square feet.
- Racking systems: Warehouses typically feature pallet racking to maximize vertical storage space and facilitate easy access to goods.
- High ceilings: Warehouses have high ceilings to accommodate tall racking systems and allow for optimal use of vertical space.
- Large walking areas: Warehouses are designed with wide aisles to enable workers and equipment to move around efficiently.
- Limited climate control: Most warehouses, except those storing temperature-sensitive goods, are not climate-controlled. They are hot in the summer and cold in the winter and require equipment to handle this harsh environment.
- Forklifts and other material handling equipment: Warehouses use forklifts, pallet jacks, reach trucks, conveyor systems, and more to facilitate the handling and movement of goods.
- Yard space: Warehouses often have yard space for loading and unloading trucks and storing overflow or oversized goods.
- Dock doors: Dock doors are standard features in warehouses, allowing for easy loading and unloading of goods from trucks, rail transport, and other vehicles.
What are the different types of warehouses?
Understanding the common characteristics and types of warehouses is essential for businesses looking to optimize their supply chain management operations.
- Distribution centers: Distribution centers serve as hubs for receiving, storing, and distributing goods to retail locations or customers. They focus on the rapid movement of goods rather than long-term storage.
- Retail warehouses: Retail warehouses store goods that are directly sold to consumers. These warehouses may include showrooms or sales floors where customers can view and purchase products.
- Climate-controlled warehouses: These warehouses maintain specific temperature and humidity levels, making them suitable for storing temperature-sensitive goods, such as food, pharmaceuticals, and other perishables.
- Bonded warehouses: Bonded warehouses are secure storage facilities where imported goods can be stored before customs duties are paid. These warehouses are typically government-regulated and provide a temporary solution for businesses dealing with import/export regulations.
- Automated warehouses: Automated warehouses leverage advanced technology, such as robotics and automated storage and retrieval systems (AS/RS), to optimize the storage, retrieval, and handling of goods with minimal human intervention.
What Activities Take Place in a Warehouse?
Warehouses are bustling with various activities encompassing the entire process of handling goods, from picking and packing to receiving to shipping. Many of these operations still rely on manual processes, paper-based systems, and Excel spreadsheets, which can lead to inefficiencies and errors.
Key warehouse activities include:
- Receiving: Warehouses receive goods from manufacturers or suppliers, inspect them for accuracy and quality, and record their arrival.
- Putaway: After receiving, goods are placed into designated storage locations within the warehouse, following an efficient organization system.
- Picking: Workers retrieve items from storage locations based on customer orders or shipping requirements, often using picking lists or handheld devices.
- Packing: Once picked, items are packed securely to protect them during transportation and ensure accurate customer delivery.
- Shipping: Packed goods are loaded onto trucks or other transportation vehicles, and shipping documentation is prepared, including bills of lading, packing slips, and shipping labels.
- Inventory management: Warehouses continually monitor and manage inventory levels to maintain accurate stock information and prevent overstocking or stockouts.
- Returns processing: Warehouses handle returns from customers, inspecting returned items for damage or defects and processing refunds or exchanges as needed.
These activities highlight the complexity of warehouse operations, emphasizing the need for streamlined digital solutions to improve efficiency and accuracy in today's competitive retail landscape.
Insights from Getac’s Experts
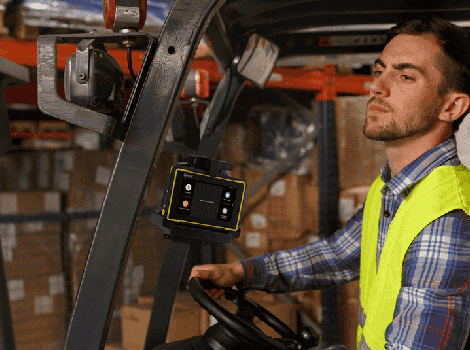
How Driving Safety Software Minimizes Distracted Driving
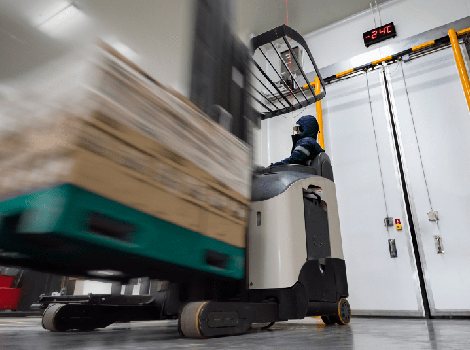
Why Rugged Solutions Are The Better Option for Cold Chain Management
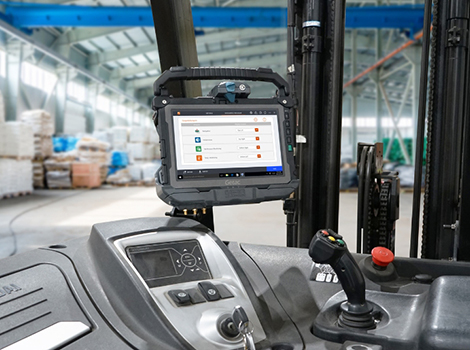
Improving Warehouse Operations Through Optimised Material Handling
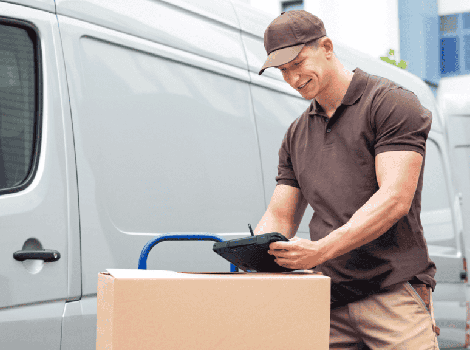
How Rugged Mobility Improves Supply Chain Efficiency
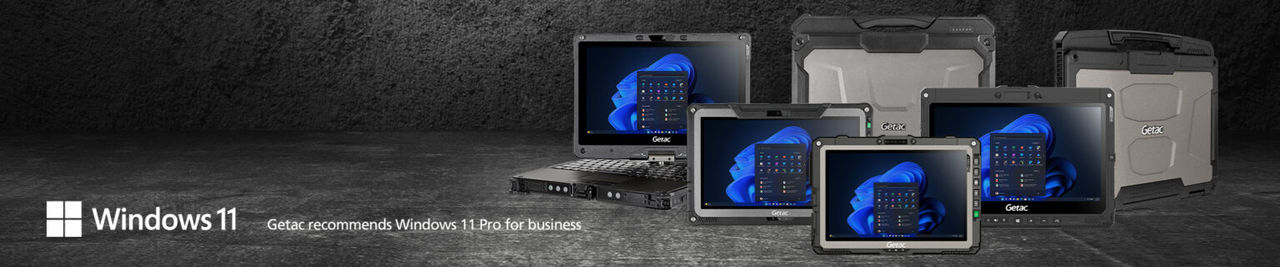