As one of the leading rugged computer providers, Getac offers extensive rugged computing product lines and serves a wide range of vertical markets.
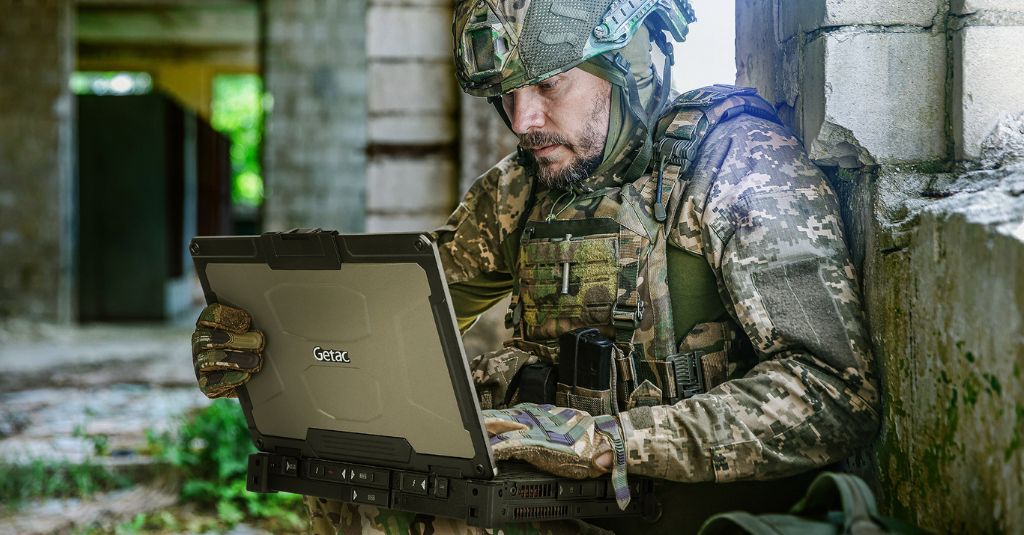
Despite the recent progress, there is still work to make heavy industries safer places to work. Workers in construction, mining, manufacturing, transportation, and in the oil & gas industry work at height or in confined spaces, risk an accident with vehicles and machines, or need to work with hazardous chemicals. Utilizing technology advancements can help to improve workplace safety even in these potentially hazardous environments.
Training in virtual reality or using robotics is one of the most efficient ways of improving workplace safety, followed by sensors, detectors, and workers’ well-being tracking wearables. However, the environments of heavy industries do pose additional requirements to the technologies. They must be durable and usable from the deepest of mines to the highest of constructions and oil rigs and fulfill all needed rules and regulations.
While the last few decades have seen sweeping advances in workplace safety, there is still room for improvement. Millions of people suffer injuries from workplace accidents every year at a high cost to themselves and their employers.
Sources: International Labour Organisation, Eurostat, Bureau of Labour Statistics, OSHA Europe, NSC.org
However, there are many ways to increase safety at the workplace, one of them is through different technological advancements. According to research by Karakhan, Xu, Nnaji, and Alsaffar (2018), higher rates of technology implementation can improve safety levels. The most apparent technology solution is the usage of robotics and other automated equipment to avoid having workers perform dangerous tasks. But the options go beyond that, from virtual reality training to workers’ health monitoring wearables,
such as smart helmets, sensors, and watches.
However, you can’t use unfamiliar technology. The National Safety Council (NSC) surveyed Environment, Health, and Safety (EHS) professionals and found that the most significant barriers to workplace safety technology implementation are:
To help companies make their workplaces even safer, Getac wanted to bridge the information gap about suitable workplace safety technologies, focusing on the following areas:
We concentrated on heavy industries such as construction, manufacturing, mining, and oil & gas for this study. As seen from the latest available workplace-related, non-fatal, and fatal injury data from Eurostat below, there is much room for improvement.
Source: Eurostat
We also included the transportation industry in this report, as we noted a relatively high rate of injuries.
Eurostat lists the oil industry under manufacturing, so individual data wasn’t provided. But according to IOGP, the International Association of Oil & Gas Producers, there were 31 fatalities in 2018 and 2,970 injuries from their member companies. These numbers would put the industry behind electricity.
We also looked at how the number of injuries reported in these industries has changed in recent years.
Source: Eurostat
Source: Eurostat
As can be seen from these graphs, non-fatal accident reductions have stagnated in some industries, with the number of injuries even increasing slightly. These industries are thus prime candidates for new workplace safety measures.
Based on various studies, reports, and articles about workplace security across the chosen industries, we could identify multiple hazardous situations which put workers at risk of injury. This is visualized in the image below. Categories relied on National Safety Council (NSC) 2019 report definitions.
Furthermore, based on industry-specific studies, such as those by Muthukumar, Janardhan, and Rajiev (2019), Hermanus (2007), and Bhattacharya & Pramanik (2020), we’ve further highlighted which hazardous situations are prevalent. Many of the most common dangerous problems are commonplace in all or most of the industries concerned. This further emphasizes the need to take workplace safety matters seriously.
Along with data from the US Bureau of Labour Statistics, the NSC interviewed 32 EHS professionals from different industries. The participants mentioned work at height (50% of the interviewed said), electrical work (50%), machinery operation (34%), heavy equipment operation (25%), and confined space entry (25%) to be the most hazardous situations in their workplaces. Other relevant categories for these industries, as were also fitting with the most common injuries mentioned in other studies, were
Like the NSC report, we further categorized risk factors for each hazardous situation as primary or secondary. Immediate risks are directly associated with the event in question, such as a falling when working at height.
There can, however, be more reasons behind the primary risk, as in why the person fell in the first place. Many of the studies and articles mentioned the following secondary factors that could create a hazardous situation:
It’s hard to find one single solution to tackle these factors. Many of them reflect the attitudes of the whole organization towards workplace safety. Their impact needs to be considered, and luckily many technological solutions can help diminish the effect of these secondary factors.
After identifying the most common safety hazards in the chosen industries, we mapped them with suitable technical solutions. As the focus of this report is on technology, standard protective equipment such as hard hats, harnesses, or rugged work boots are omitted.
From looking into interviews and surveys on EHS professionals about safety technologies, we got an idea of what technologies the professionals themselves are already using or would like to use more frequently. The professionals interviewed by the NSC mentioned a long list of technologies they are already using:
The interviewees could give more than one technology in their response. So the percentages correspond to the number of participants who mentioned the technology and will total above 100.
Based on an interview by the research and advisory company Verdantix, EHS professionals think these three technologies show the most potential:
Automation through robotics proved the most common technology, followed by various sensors and software. The growing interest in virtual and augmented reality is also understandable, as these technologies have gained more media popularity. Training for hazardous situations through virtual or augmented reality was also mentioned in various studies across industries as a great way to prepare workers for possible dangers safely.
Artificial intelligence (AI) refers to computer-equipped machines operating large data sets through algorithms, enabling them to perform tasks or solve problems on their own. Intelligent industry machines can thus learn from the data given to them and be able to provide predictions for possible future scenarios.
Augmented reality (AR) allows a person to experience the world with augmented sensor inputs, such as computer-generated overlays or forms. AR can be used to send worker safety information (e.g. training materials) to be viewed via devices like special glasses.
Automation and robotics refer to equipment or machine designed to perform tasks partly or entirely instead of the worker. Examples are drones, semi-automated vehicles for moving items, or robotic drills.
Big Data refers to analysing and extracting information from data sets too big for traditional data analysis software. It can be used to gather and analyse machine or worker well-being information, for better decision-making.
Virtual reality (VR) provides a computer-generated interactive simulation of a scenario. In virtual reality safety training, the worker can go through a simulation of an accident situation realistically and stay completely safe.
Analyzing data from industrial machines to the working environments can only be expected to become even more popular in the future. Machine malfunctions or adverse weather can more easily be anticipated through analytics. Also, monitoring workers’ well-being through wearables can help to reduce risks associated with fatigue.
However, some technical solutions more effectively increase safety than others. From the data, we could establish a hierarchy of technological effectiveness to determine which solutions one should concentrate on:
This graph shows that moving the worker ultimately from the potentially hazardous situation can help make the most significant improvement in workplace safety. According to the research of Cameron & al. (2018), the increased usage of robotics and automatically driving vehicles, such as drones, can help to reduce workplace-related injuries by up to11% by 2030. Drones and robotics won’t just allow the worker to step away from dangerous situations. These machines can also take care of dull and repetitive tasks. This, in turn, could help keep workers more alert during the working day and diminish the risk of injuries related to fatigue or carelessness.
The next-best options are engineering or admin controls such as sensors and barriers and other data-collecting items like wearables. Digital devices can also help workers pay more attention to safety workflows and procedures in their workplace. Employees can get reminders to wear protective equipment through their wearables or notifications when entering hazardous areas.
The least effective safety technologies are smart PPEs, or technology-enhanced personal protective equipment, such as smart helmets, smart glasses, or fatigue monitors. They can send information about workers’ well-being straight to managers.
Wearables and smart PPE are intelligent wearable technologies that obtain information about a worker’s surroundings, location, or well-being. Examples are watches, smart helmets or sensors on vests, which can send alerts for hazardous gas exposure, signs of fatigue or information about working posture and vital signs.
However, these sensors and PPE are only effective when used correctly. If a worker does not stop to take a break even when their smart PPE tells them to, the equipment can’t be said to have had any positive impact on workplace safety.
Below, based on the framework from the NSC report and further studies and articles on technologies used in manufacturing, construction, transportation, mining, and the oil & gas industry, we’ve created the following visualization of relevant technologies for each of the most common hazardous situations.
We’ve used the hierarchy for the different solutions better to visualize the effectiveness of each solution for each risk.
Users can employ certain technologies to address multiple different risks. For example, as fatigue is a common secondary risk factor in many hazardous situations, wearables for tracking employee fatigue levels are often present in the graphic.
This graphic gives an overview of the different technologies available even beyond the industries observed in this report. However, as the heavy industries in this study are all unique, we’ve also illustrated efficient technologies and their use cases individually for each industry as well.
Permit to work technology provides access to certain areas or permission to work on certain tasks only to authorised personnel. Software can be used to make sure that only people with the required training and certification can perform certain tasks, such as handling dangerous substances.
Most factories today are partially automated, but the benefits of technology to manufacturing don’t stop there. Through IoT sensors, managers can receive real-time data from the machines and be alerted when maintenance work is needed.
IoT or Internet of Things refers to physical objects, such as connected vehicles, attached with sensors, monitors, and processing software, to connect & send data to other devices via the internet. It enables people to monitor the work of machines and equipment remotely and to use automated controls such as off-switches for the entire work environment.
Other trends in manufacturing indicate a multitude of different technology solutions. such as high-technology wearables to monitor workers’ posture and the noise level of the factory floor. Another promising possibility is virtual reality programs to train workers to deal with hazardous situations and accidents. Getting clothing or body parts entangled in a machine is extremely dangerous. Wearable sensors can alert workers if they are standing too close to a device or otherwise not following safety protocols.
With fatigue-monitoring wearables, workers can have breaks when needed or have high-concentration demanding tasks when they are the most alert, according to the fatigue data.
According to recent studies and research, there is plenty of room for improvement in safety technology in construction. This is because the construction industry generally lags behind other industries in technology adoption. However, the industry can benefit from different technologies in multiple ways, presented in the graphic below.
Organizations can use VR training to train workers about complex or dangerous tasks. Doing so would better prepare them and decrease the risk of accidents and injuries.
Software such as 3D/4D computer-aided design (CAD), building information modeling (BIM), and laser scanning can help identify hazards from afar.
Proximity sensors can reduce the risk of collisions or falls. This technology can alert workers when an object, such as a piece of machinery or a person, enters set proximity.
Location geofencing detection can alert workers when entering a potentially dangerous worksite zone. This limits accidents arising from disregarded safety procedures in high-risk areas. Work zone intrusion detection will alert workers if unauthorized people enter the work area without permission.
Robotics and automation, such as crewless aerial vehicles, can be used when work needs to be done high above the ground.
Wearables can monitor lone workers, prevent collisions with machines and help to find all employees faster in an emergency. They can also help prevent or reduce health risks from too long an exposure to high temperatures during hot work.
3-D/4-D computer-aided design (CAD) uses the help of computer technology to design or create technical documents in either three or four dimensions. It helps engineers and architects better visualise the construction process and identify potential errors in the plan.
Building information modelling (BIM) can use laser scanning to accurately create a digital presentation of a physical building or a construction site. It can be used to identify and assess potential hazards safely from afar.
Proximity sensors will sense if an object or a human gets too close to another object or human or enters a restricted area.
Location geofencing triggers an action when a device enters a set area. It can be used to alert workers through apps or wearables that they are about to enter a restricted or hazardous area at work, or to stop unauthorised people from entering a construction site.
The most used safety technologies in transport are sensors, cameras, and devices monitoring obstacles and speed.
Also, in transportation, eliminating the human factor with crewless vehicles such as connected vehicles (CV) or automated vehicles (AV) can significantly reduce road accidents. Organizations in the industry can employ software installed in cars. This will help stop drivers from using digital devices and demand them to stop for breaks.
Key data needed for crossing borders can be saved conveniently on digital devices, helping avoid stress and long waiting periods at customs, while benefiting the worker’s well-being.
Also, VR training can prepare drivers for various hazardous driving scenarios and protect them in a dangerous situations on the road.
For mining, the most mentioned and therefore most effective technologies are the ones that can help to remove the worker from potentially hazardous situations or to alert them.
Worksite simulators can be used to provide training without exposing inexperienced workers to hazardous environments.
Robotics and automation such as self-driving trucks or robotic drills enable workers to step away from hazardous situations and environments. Drones can be used to take images inside mines in areas with the risk of collapse and replace labor-intensive survey, inspection, or mapping activities.
Sensors and monitors can also help make mining safer. By monitoring rock movements, workers can receive warnings regarding the potentially dangerous seismic activity. Radar can identify workers underground and assist in planning drilling and controlled demolitions. Monitoring usage patterns of heavy equipment through radio-frequency identification can aid the scheduling of part replacement or fluid change or maintenance optimization.
Wearables can also benefit workers in multiple ways. They can detect
environmental hazards, including poor air quality, and emit a warning signal early on for
potentially harmful or dangerous situations. They can also help locate workers in mines during an emergency and keep tabs on their fatigue levels.
Radio-frequency identification (RFID) uses radio waves to transmit information about objects or to locate people. It can be used to track lone workers in a mine or to monitor usage of heavy equipment for possible repairs.
As in other industries, drones and robotics can help prevent accidents while extracting oil and gas. They can be used, for example, in oil tank inspection or other dangerous maintenance jobs to get a better overview of the site.
IoT can be used to gather data from machines and keep an eye on performance. Monitors can be placed on-site to track the levels of hazardous gases in the air. This is especially important in confined spaces. Additionally, the oil and gas industries’ GPS systems and other wearables can help to track employees’ location and well-being on-site, even onshore.
Special attention has also been given to vehicle collisions. These make up a significant proportion of accidents in the industry due to the long distances involved. Technologies like radar, 360-degree cameras, digital device usage blocking software, or fatigue-tracking wearables can help improve safety when driving from site to site.
The heavy industries studied in this report pose specific strains for people and the equipment used in the industries. EHS professionals interviewed in the NSC survey were especially concerned about the different technologies’ adaptability to their industries’ special requirements. Thus, equipment used in these working environments needs to be specially equipped for unique stresses.
First, devices must be robust and able to take hits or drops. Of course, when a person accidentally falls from a height, what happens to the device they carry is unimportant. But if workers know their device can withstand a fall, they will not reflexively try to catch it. This poses a risk of them falling after it themselves.
Devices must also work correctly in diverse conditions. A mine or construction site can be filthy and loud. Therefore, the products used in these environments must be able to stand dust, sand, vibrations, and moisture build-up. Additionally, at oil fields or construction sites, there might be minimal cover from sunlight. For workers to follow visually-prompted instructions, the screen must be bright enough to be visible under direct sunlight.
All workplaces must comply with the laws and regulations of the country in which they are operating. The European Union also has a list of directives related to safe and healthy working environments, which its member states must consider.
The workplaces in the industries chosen for this study can also further be classified as hazardous work environments. Working in mines, on oil rigs, or transporting dangerous substances such as gasoline pose an increased health and safety risk for the workers, making it crucial that equipment used in these environments doesn’t add to that risk.
For example, in America and Europe, all products and equipment used in hazardous environments with potentially explosive atmospheres must be certified. Certificates such as UL and C-UL in North America and ATEX in Europe ensure products are used in workplaces with potential fire or an explosion.
ATEX is the EU directive for the required safety procedures needed in hazardous environments where a risk of an explosion is present. It sets special requirements for all equipment used in these environments.
UL/C-UL are globally recognized certifications for products used in hazardous environments granted by the North American company UL.
Safety products cannot get in the way of everyday work. They need to be light and easy to carry in a tight mine elevator or climb a construction ladder. Employees also must use or wear them alongside their regular safety gear. Items like touchscreens must be usable while wearing gloves.
In hazardous environments, it’s essential that teams communicate back and forth, below and above ground (mines) or on land (oil rigs). The devices one uses must have long battery life and strong WiFi/4G/LTE signal. In environments where it’s impossible to get a signal, other ways of transporting data and information such as Bluetooth must be standard.
Deep in a mine or high above the ground on a construction site, or with a flat tire in the middle of nowhere, it’s essential that employees are reachable and need not struggle with their devices. GPS makes it possible to track employees, especially if they need to work alone, further increasing worker safety.
It’s impossible to prevent workplace-related injuries completely. However, several technologies are available for companies of different sizes to improve workplace safety.
Many of the most effective technologies for preventing workplace injuries are the ones that aim to remove the worker from the dangerous task altogether. Automation replacing human workers is often perceived rather negatively. However, it should be welcomed in cases where it can improve workplace safety.
However, technology has its limits. Many injuries are the result of human error, such as negligence of safety procedures or fatigue. Monitors, wearables, and reminder apps can help workers to remember to use their protective gear. Such devices help managers to monitor employee levels of alertness. However, it’s the managers’ job to organize shifts and working procedures to ensure employees stay as safe and alert as possible.
Similarly, it’s managers’ job to ensure workers have the necessary skills, as insufficient and inadequate training poses a significant risk. Something unexpected can always happen, but thanks to technology, one can be prepared. With virtual and AI training, workers can safely practice for hazardous situations and be ready if something goes wrong.
Lastly, new technologies must be able to adapt to the specific needs and requirements of different industries. The devices must comply with the rules and regulations set by other countries, states, and global organizations. These devices can’t become risk factors, for example, in explosive environments. Manufacturers of these technologies must be aware of all these risks and what these environments are like to improve workplace safety truly.
Hermanus, M.A. (2007), Occupational health and safety in mining—status, new developments, and concerns”, Hermanus, The Journal of The Southern African Institute of Mining and Metallurgy
Horton J, Cameron A, Devaraj D, Hanson RT, Hajkowicz SA (2018) Workplace Safety Futures: The impact of emerging technologies and platforms on work health and safety and workers’ compensation over the next 20 years. CSIRO, Canberra.
Karakhan A., Xu Y., Nnaji C. and Alsaffar O. (2018), Technology Alternatives for Workplace Safety Risk Mitigation in Construction: Exploratory Study, Conference: Proceedings of the 35th CIB W78 2018 Conference: IT in Design, Construction, and ManagementAt: Chicago, IL
National Safety Council, 2019, Safety Technology 2020: Mapping Technology Solutions for Reducing Serious Injuries and Fatalities in the Workplace.
TOP 5 SAFETY INNOVATIONS IN MINING
Five Ways Hazards Are being Combated In The Oil & Gas Industry
Subscribe below to be kept up to date on the latest industry and technology trends. We will send you a monthly blog round-up direct to your inbox.