Stefan Doepp has broad experience in IT projects, having worked in the industry for over 20 years. He is the Enterprise Account Manager at Getac Technology GmbH, working in the sales division for industrial customers.
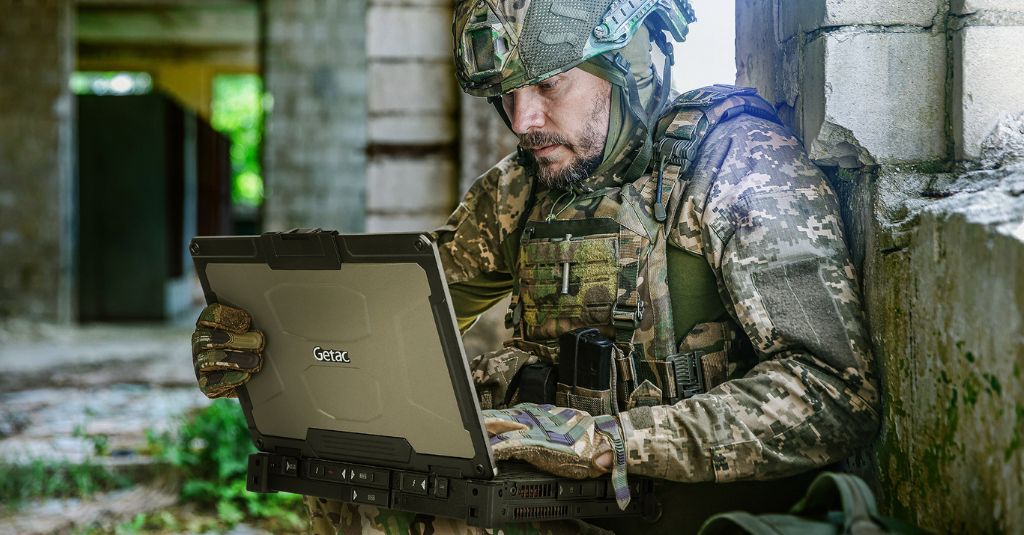
Getac Select
A combination of rugged computing devices, software, accessories and professional services in a purposeful range of specifically tailored solutions.
Getac Video Solutions
Video capture, evidence management, rugged hardware and robust software solutions for law enforcement and other industries.
Defense
Mission-critical COTS computing that delivers high powered processing and reliability in operational environments
Public Safety
Law Enforcement, EMS, Fire & Rescue applications
Utilities
Smart Meter Reading and Installation, On-site Safety, Utility Asset Management, Workforce Management for Utilities, Mobile GIS, Surveying and Mapping
Transportation & Logistics
Railroad Management, Airport Management, Port Management, Long-haul Delivery Fleet Management, Warehouse Materials Handling
Industrial Manufacturing
Industrial Programming and Robotic Control, Facility management, Compliance and Inspections, Workforce Management, Inventory and Warehouse Management, Factory Automation and Plant Monitoring, EAM and CMMS Solutions.
Automotive
Optimized Rugged Mobile Solutions to drive a smarter approach throughout the automotive value-chain.
Natural Resources
Mining, Forestry and Construction applications
Oil & Gas
Remote Support, Asset Management, Field Data Analysis, Workplace Safety
It is no secret that digital transformation is revolutionizing many industries, including manufacturing. The excitement surrounding the digitizing of manufacturing is that old workforce management processes can now be made more transparent with data and that data can guide practically every decision, large or small.
In Industry 4.0, the prescribed data guidance happens through a variety of advanced technologies, the Industrial Internet of Things (IIoT), artificial intelligence (AI) and machine learning (ML); and augmented reality (AR) are just a few — all of which work together to deliver a smart factory. These technologies also positively impact one of every factory’s most vital assets: its employees. Through rugged and mobile devices on the plant floor, workers can access insights from various technologies, illuminating the results.
Here’s what Industry 4.0 can do for your talent:
Industry 4.0 is a broad term used to describe modern development of manufacturing processes through technology. These changes and developments work to build smoother manufacturing processes than ever before.
Industry 4.0's digitization of processes can improve workforce management procedures. Workers on the plant floor who can access their company’s ERP and EAM software on rugged mobile devices need not waste time trekking to a desktop computer to schedule manufacturing tasks or request time off.
Pen-and-paper solutions can also get misplaced or damaged on the plant floor. Industry 4.0 helps bring the work to the employees instead of the employees to work. This can significantly improve efficiency and uptime. Easy scheduling of tasks and insight into order and workflow management through on-floor access to your ERP makes employees invested in your processes and outcomes.
Transparency is another one of the many benefits of Industry 4.0. Entire companies can use that transparency to facilitate easier data access, improving productivity. It also helps that today’s workers are already familiar with mobile devices for personal use, so adoption at work is extremely manageable for a large amount of Industry 4.0 solutions.
Industry 4.0 AI and ML can help with predictive maintenance, reducing the amount of downtime on the plant floor. But when machines do fail or look suspicious, you might need to rely on expertise from original equipment manufacturers or even in-house personnel. Unfortunately, frequently relying on experts can negatively impact the bottom line.
Augmented reality (AR) functionality on mobile devices cuts down travel time and makes wiser use of expertise. AR imposes a digital layer of a part over an actual scenario. Through shared video calls and AR on the tablet on the plant floor, the expert and machine operator can communicate counsel and troubleshoot live as the asset is in operation.
Such AR solutions are beneficial when a bank of experts has to service multiple locations in multiple geographies. Instead of traveling to each location and increasing downtime, AR solutions can efficiently facilitate remote dial-ins and expertise sharing. While AR technology is still in the early stages of development within Industry 4.0, the manufacturing industry, especially the automotive sector, is already taking it for a test drive. Grand View Research predicts the global market for AR across all market segments will grow at an astounding 74.9% compound annual rate to reach USD 100.2 billion by 2024.
Imagine reading a paper manual offsite and then figuring out how to work a machine on the plant floor. While shadowing current workers helps new employees ramp up to work, the process is inefficient, with many stops and starts. Safety regulations in manufacturing also mandate that employees pass through various mandatory training protocols before operating related equipment.
With Industry 4.0 interactive digital AR manuals loaded on mobile tablets next to each machine can do the task more efficiently. The worker can pull up the appropriate documentation and run through the training program at the station. Live AR views can give a much better visual representation of troubleshooting and workforce management operating procedures.
With Industry 4.0 systems, workers can train ML algorithms to spot defects in finished products. Such anomaly detection programs use mobile devices on the plant floor to identify where errors have occurred. In this way, employees can catch problems early before they snowball into more significant headaches. Digitized processes built for Industry 4.0 also enable workers to record information related to the problem. They can document the instance with pictures, making for a more thorough assessment of the situation. Saving reports digitally this way is also helpful to address additional issues on workforce management and facilities.
Too often, manufacturing companies have “machine whisperers”. These are experienced workers who can listen to the sound of a machine or even smell it to detect that something is wrong. They understand when and how to work with a device they have worked with for decades. Such worker expertise is invaluable. However, both discrete and process manufacturers risk losing that expertise when the employee retires or leaves the company. Industry 4.0 uses quantifiable and measurable data from machines to make data-based decisions. The data is also centrally stored and accessed. This means all workers, no matter how experienced, can access a single source of truth.
Industry 4.0 enables the collection of essential machine data through IIoT, enabling analysis through ML programs. Workers can get notified in case of problems through wearables or their mobile devices on the plant floor. Data is a vital currency in manufacturing. Making it readily available to all is one of the many advantages that Industry 4.0 confers.
Making the most efficient use of in-house talent is always vital in manufacturing. This is especially so in countries that are registering a shortage of labor to fill industry jobs. A 2018 Deloitte report, for example, found that 2.4 million manufacturing jobs will go unfilled in the United States by 2028. While such shortages are not universal, it is worth noting that worker productivity and satisfaction are tied to higher-order skills, the kind that smart manufacturing delivers.
Much is riding on the promise of Industry 4.0. The digital transformation that accompanies it can make workforce management much more efficient. It can also make for productive manufacturing companies of all sizes.
Getac’s rugged tablets and laptops are designed to meet the processing demands of Industry 4.0 while staying fully mobile and tough enough to handle extreme environments. Explore Getac rugged solutions or contact us to learn more.
Stefan Doepp has broad experience in IT projects, having worked in the industry for over 20 years. He is the Enterprise Account Manager at Getac Technology GmbH, working in the sales division for industrial customers.