Frank Baldrighi is Getac's Business Development Manager in Australia and New Zealand. Frank has over 15 years' experience in the tech industry, specializing in partner sales strategy and direct business relationships.
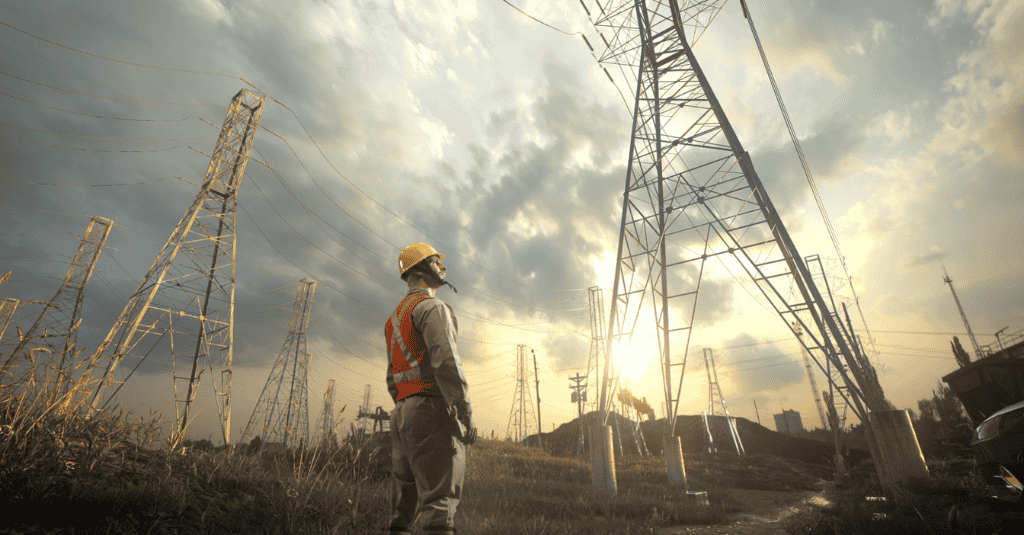
Getac Select
A combination of rugged computing devices, software, accessories and professional services in a purposeful range of specifically tailored solutions.
Getac Assist
Getac Assist is our fully rugged remote expert solution aimed at assisting field service engineers and technicians with knowledge transfer, remote guidance, inspection, quality control, safety, compliance, and more.
Defence
Mission-critical COTS computing that delivers high powered processing and reliability in operational environments.
Public Safety
Ambulance, Fire & Rescue and Policing applications
Utilities
Smart Meter Reading and Installation, On-site Safety, Utility Asset Management, Workforce Management for Utilities, Mobile GIS, Surveying and Mapping
Transportation & Logistics
Railroad Management, Airport Management, Port Management, Long-haul Delivery Fleet Management, Warehouse Materials Handling
Oil & Gas
Remote Support, Asset Management, Field Data Analysis, Workplace Safety
Industrial Manufacturing
Industrial Programming and Robotic Control, Facility management, Compliance and Inspections, Workforce Management, Inventory and Warehouse Management, Factory Automation and Plant Monitoring, EAM and CMMS Solutions.
Automotive
Optimised Rugged Mobile Solutions to drive a smarter approach throughout the automotive value-chain.
Natural Resources
Mining, Forestry and Construction applications
What value do you want to gain for your business models? Which efficiencies will make your bottom line more profitable? Digital transformation is not simply about digitising operations. Instead, it is a looping process meant to clarify these answers for every enterprise and then use technology to achieve the desired results. What applies to one company may not hold true for another, underscoring the need for tailored approaches in integrating digital technology and addressing unique business challenges.
Leveraging technology to drive profitability is not new in business operations. What is relatively new is the merging of computing power, network infrastructure, and an increase in data from fresh sources. This powerful combination makes it possible to derive insights from processes that have been opaque for a while. Even better, businesses can access the information they can act on in real-time and on the go. The number of incremental benefits quickly adds up to substantial gains in productivity. Successful digital transformation requires integrating different areas within IT and digital strategy, such as employee experience and infrastructure.
You already know that data drives business. That is especially true for digital transformation as data feeds several key technologies in its ecosystem. Rugged devices and tablets in various industries–industrial manufacturing, automotive & transportation, public safety, natural resources, and oil & gas–play an essential role in digital transformation. They serve as a platform to access information on the go and to act on insights about workplace safety.
Digital transformation is driving significant change across various industries, leading to the adoption of innovative business models and cutting-edge technologies. The ability to adapt to these changes is crucial for companies aiming to remain competitive and deliver exceptional value to their customers. While change can be challenging, it also presents numerous opportunities for growth and improvement.
Technology plays a pivotal role in accelerating change, helping companies to automate operations and enhance productivity. The modern workplace is evolving, with a growing emphasis on flexibility, sustainability, and employee well-being. Companies must navigate the challenges of integrating new systems and processes, a reality that requires a cultural shift towards innovation, experimentation, and continuous learning.
The benefits of embracing change are substantial, including improved quality, increased efficiency, and enhanced customer experience. To successfully manage change, companies must measure its impact using data and insights to inform decision-making. Leadership plays a critical role in driving change, with a clear vision and strategy essential for success. By fostering a culture of adaptability and continuous improvement, companies can thrive in the dynamic landscape of digital transformation.
Digital transformation enhances workplace safety by leveraging technology to reduce risks while supporting productivity and compliance with OSHA standards.
Since the early days of the COVID-19 pandemic, industry has learnt several key lessons:
As organisations embrace digital transformation, they face significant challenges stemming from outdated technology and processes, which can hinder their ability to initiate this critical transformation effectively.
The goal of digital transformation is to move businesses along a customised path, from adding automation process steps to fully autonomous operations. Along the way, enterprises will pass various milestones that reduce the fraction of human involvement and orchestration into the process: from done by humans, through done with humans, to done for humans.
The key for asset-driven industries is to begin with the desired goals in mind, and establish key performance indicators (KPIs) to measure progress toward those goals. The work of digital transformation involves breaking down business operations into manageable processes that can be orchestrated or automated with the help of technology.
Data, the currency of digital transformation, enables several technologies to build new capabilities and deliver enterprises’ desired results.
Some of the technologies that propel digital transformation include:
Organisations must create innovative solutions, rather than merely relying on existing systems to fully leverage these technologies.
Selecting which of these technologies best fits in asset-driven industries depends on the digital maturity of the company and the KPIs they intend to measure. Industries that need remote/in-field collaboration can employ AR and MR using rugged tablets and devices. These technologies create the technology portfolio for digital transformation.
Until recently, asset-driven industries such as manufacturing, utilities, oil and gas, transportation, logistics, and more, suffered from a data disconnect between the road and work. Employees had to call corporate headquarters or a field manager with a better view of operations. All this just to figure out which task to attend to next or where a replacement part was in the inventory. Machine parts got replaced whether needed or not, shutting down production unnecessarily. This reliance on pre-packaged solutions is shifting as IT departments focus on creating innovative capabilities rather than relying on bought software.
Digital transformation helps alleviate a few pain points for these industries. A checklist of must-haves for operational efficiencies and sustainability in these sectors includes:
5G can transmit a higher volume of data at faster speeds, enhancing real-time decision-making and operational efficiency while reducing latency and lag.
Since industries like industrial manufacturing, automotive & transportation, public safety, natural resources, and oil & gas often work with ageing infrastructure, collecting and analysing data in their various business operations usually uncovers recommendations to boost efficiency. The gains come from applying trends from data collected from operational technology (OT) and integrating them into IT processes. Tying IT and OT more closely does pose various challenges, including data usability and formatting, data security, messaging and device compatibility, and addressing hazards, but forms one of the foundations of digital transformation.
Efficient operations design workflows to send a job to the worker. As a result, team members need to access insights in the field and can not be constrained to a desktop. Digital transformation impacts their day-to-day work and interactions significantly, making it essential for leaders to create a supportive environment for higher performance.
Workers who access information remotely need devices that can withstand the rigours of harsh environments. Rugged devices deliver efficiency and effectiveness in these harsh environments, ensuring that IT can respond to business needs promptly and reliably with no performance drop-off.
Remote workers need access to the same information as everyone else in the enterprise. One of the promises of digital transformation is that it enables real-time insights, minimising the time to employ corrective action. As a result, all information must be accurate and centralised so that the entire team observes the same trends. It is crucial to create centralised and accurate information for all employees to ensure consistency and reliability.
A higher level of digital maturity allows a higher degree of automation up and down the value chain. This digital maturity allows companies to grow their operational efficiencies, enabling them to keep pace with evolving technological demands and increasing profitability in kind.
In the ideal state, digital transformation needs only a light touch from humans, allowing workers to verify machine performance from remote locations and manage entire fleets of operations. It fundamentally alters how businesses operate, enabling them to efficiently manage remote operations and increase the value they provide to customers.
Occupational safety is a critical aspect of workplace safety, with companies bearing the responsibility to protect the health and well-being of their employees. The Occupational Safety and Health Act (OSHA) mandates that companies provide a safe working environment, free from hazards and risks for its staff. Regular risk assessments are essential to identify potential hazards and implement measures to mitigate them.
Employee training and education are vital for promoting workplace safety, ensuring that workers are aware of potential risks and know how to manage them effectively. In certain industries, such as mining and construction, the use of personal protective equipment (PPE) is crucial. Companies must also have procedures in place for reporting and investigating incidents, focusing on learning from mistakes and improving safety protocols.
Workplace safety is not just a moral imperative but also a business-critical issue. The cost of injuries and illnesses can significantly impact productivity and profitability. Companies must demonstrate a commitment to workplace safety with clear policies and procedures.
The use of technology, such as automation and robotics, can enhance workplace safety by reducing the risk of human error and injury. Balancing the need for productivity and efficiency with the need to protect employee health and well-being is essential for sustainable business operations to meet OSHA requirements and standards.
Beyond OSHA, digital transformation requires compliance with data privacy, security, and competition. There are industry-specific guardrails, in addition to those that aim to promote a fair and open market to reduce market concentration. Digital transformation can be a differentiating factor for a company, but it must not hinder the ability of the market to include new entrants for consumer/customer benefit.
In addition, regulations to promote transparency regarding how user data will be used or sold must keep pace with technological advancements, while also ensuring that cybersecurity practises are followed to prevent unauthorised access to users’ data.
The use of software and other tools can help companies manage regulatory compliance by providing a framework for tracking and reporting incidents. Demonstrating a commitment to regulatory compliance involves having clear policies and procedures in place. And while the cost of compliance may be significant, the cost of non-compliance can be far worse, with companies facing fines and penalties for failing to meet regulatory standards.
Navigating the complexities of regulatory compliance requires a thorough understanding of the requirements and obligations. External experts and consultants can provide valuable guidance and support. Balancing the need for regulatory compliance with the drive for business growth and innovation is crucial. Leadership plays a critical role in ensuring regulatory compliance, with a clear vision and strategy essential for success. Partnering with a supplier that incorporates regulatory compliance into their technology can provide peace of mind that moving to a digital-first approach won’t risk non-compliance. By adhering to regulations, companies can protect their employees, avoid costly penalties, and foster a culture of safety and responsibility.
Rugged mobile devices play a key role in digital transformation by enabling real-time data access, efficient workflows, and future-ready AI integration in harsh environments.
Predictive machine maintenance is one of the many exciting possibilities of digital transformation. The process as follows:
Predictive maintenance is not the only bottom-line boost that digital transformation delivers. Perhaps the biggest promise of digital transformation is that it can be applied to practically all operations across an enterprise. Small gains in efficiency add up to significant savings. Determining the effectiveness of digital transformation investments is crucial to ensure that the underperformance of individual projects does not negatively impact overall efforts. In this sense, digital transformation is a continuous improvement process, not a one-time event. However, resources should be spent strategically, considering the unique needs of different employee segments to avoid squandering investments.
A logistics company, for example, can use artificial intelligence to proactively tell when package labels are not glued on and adequately alert vendors who repeat the pattern. They save time by avoiding the need to reroute packages to workers who must correct improperly addressed ones. In the field, workers can utilise data from individual utility trucks to optimise routes and plan schedules for their fleets. Inventory management can be automated, and supply chain anomalies are identified more quickly with the aid of automation and machine learning models. The possibilities with digital transformation are endless.
Beyond more efficient business operations, data-driven digital transformation can highlight bottlenecks across all departments in organisations, enhancing operational efficiency metrics. A well-structured guide is essential for developing effective digital transformation strategies, providing a pathway for organisations to follow.
Companies can deploy workers strategically and access opportunities to deliver superior customer service. For example, field service on the road can find replacement parts from other road operators, reducing potential injuries instead of rescheduling service calls.
According to a McKinsey research report, 70% of enterprises that had pursued digital transformation reported in 2020 that their momentum had stalled. It is worth understanding the reasons–culture or scale for example–causing the slowdown as payoffs can be impressive. Digital transformation can lead to more efficient operations, with enterprises enjoying autonomy beyond their operations. An entire ecosystem with data transparency functions more smoothly as inefficiencies are easier to pinpoint and fix.
Businesses must also watch market trends and shifts in consumer behaviour to adapt and thrive in the evolving landscape. The 2024 update to McKinsey’s tech trends focused on generative AI, coupling with electrification and renewables in terms of interest and investment. Gen AI is the next step in digital transformation, and can and should enhance nearly all performance metrics. Reacting and optimising data automatically will take the advantages of digital transformation and accelerate them even faster.
Rugged mobile devices (especially AI-capable) contribute an invaluable benefit to the digital ecosystem. They connect workers to vital information necessary to keep operations running in harsh environments, often where and when workers need the data most. Employees can use a rugged mobile device for asset management software or enterprise resource planning systems to troubleshoot problems quickly and efficiently whenever worker intervention is called for. Using rugged mobile devices also allows for the easier digitised recording of processes, so the enterprise always has a record related to every machine.
Looking to leverage advanced technologies, enterprises are taking a careful look at their business operational workflows and finding ways to improve the bottom line. In the future, expect AI-fuelled digital transformation to become a mindset for enterprises as they move toward autonomy in their digital transformation. Rugged mobile devices will be essential today and even more so tomorrow to future-proof technology fleets. Their secure and open architecture enables enterprises to use it as a communications platform now and into the future.
Frank Baldrighi is Getac's Business Development Manager in Australia and New Zealand. Frank has over 15 years' experience in the tech industry, specializing in partner sales strategy and direct business relationships.